Automate or Improve: Why choose?
With the advent of Intelligent Automation (IA), and particularly Robotic Process Automation (RPA), businesses are often opting to automate processes as-is, rather than spending some initial time optimising their processes through more traditional process improvement. So with businesses achieving rapid returns on applying automation in their current states, often quickly automating a task or process before moving on to the next in the backlog, why should they invest more time on a process than is required?
The benefits of optimisation
Intelligent Automation in itself doesn’t re-design anything, it doesn’t explore whether a process step or task is value-adding or not, it doesn’t examine the level of quality or rework in a process, or if it’s having an adverse impact on customer experience. Not spending the time doing the proper analysis and implementing improvements, results in missed efficiency opportunities.
As well as missed opportunities for improvement, automation cost more than they need to. For example, if a process hasn’t been properly reviewed in years, it’s very likely some of the process steps or business rules don’t make sense in the current environment. By not taking time to remove these wasteful steps you could be automating a poor process – see example below:
The cost of automating an inefficient process
But does that matter if a bot is now going to do all the work? Well, yes. Longer, complex processes typically translate to a more complex automation build and higher overall maintenance cost:
- As a rule of thumb, development complexity is linked to how long it would take a human to do a task (i.e. the number of clicks, moves, and working between applications) so these would need to be recreated within the automation development. If we use the above example of automating the current state, which has a cycle time of 15mins, this could take 3 times as long to automate versus the simplified 5-minute process.
- Managing more complex automations in production typically translates to higher maintenance costs as the chances of bug fixes or change requests are much higher.
- From an infrastructure perspective, longer processing times equate to more bot time, meaning higher license and cloud computing costs.
A joint optimisation and automation approach
The below diagram details how optimisation can be introduced to your current automation lifecycle:
To determine whether a process should be optimised we look at some of the key process characteristics, including:
- Level of rework
- Bottlenecks or obstacles (contributing) to process inefficiencies
- Variation of inputs, outputs, and overall process
- Duplication of effort
In summary, it’s best to invest the time in doing process re-design while implementing IA. This can not only lead to reductions in the time and cost of the overall initiative, but also improve the ROI compared with IA implementations with no process change.
At Kainos, we combine our expertise in Lean Six Sigma methodologies and Intelligent Automation to deliver fully optimised solutions for our clients. If you want to know more, then contact us and find out how we can help you achieve your business goals through automation and optimisation.
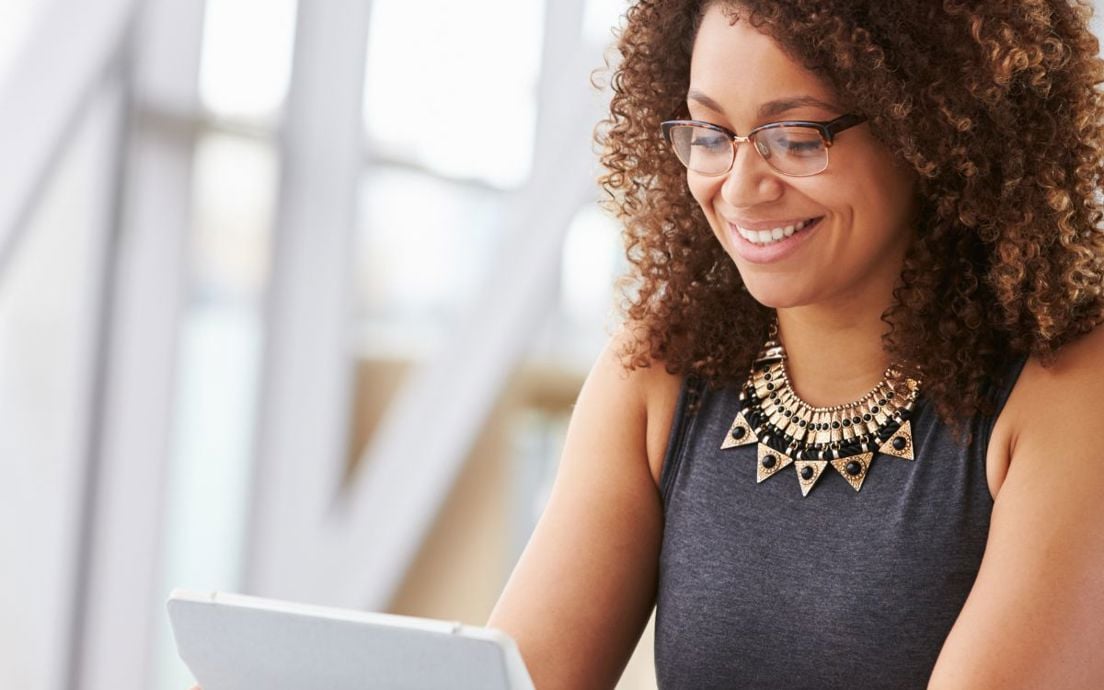
Interested in learning more?
Download our whitepaper to discover how Intelligent Automation can help transform your organisation.